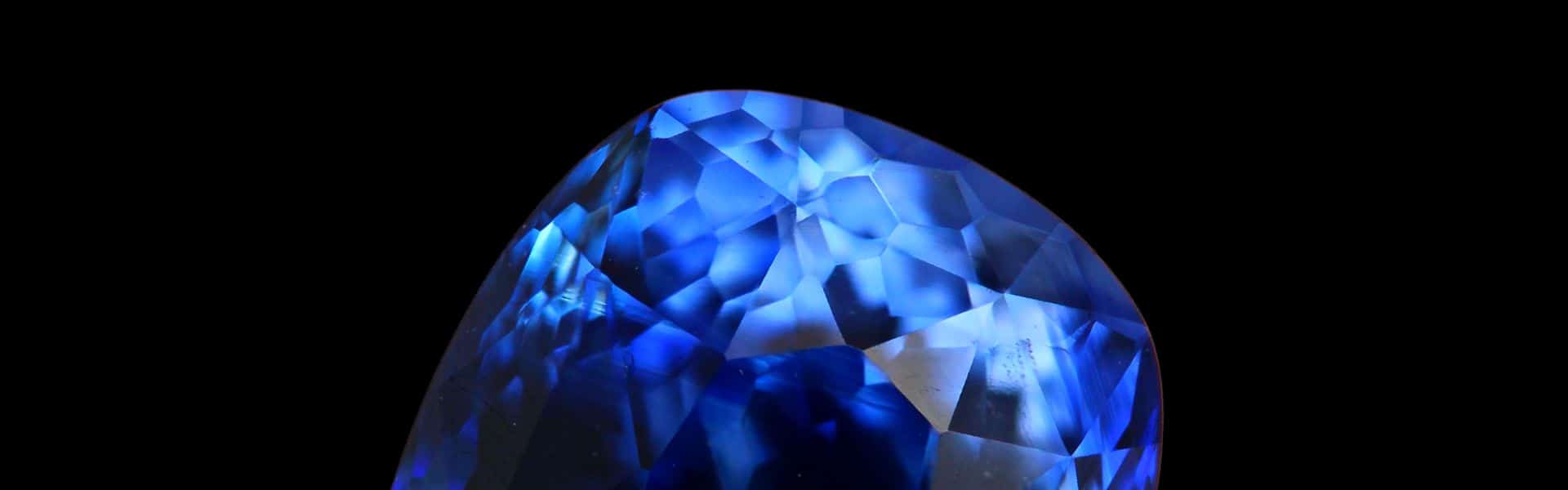
Flotation Process in Metallurgy: Unlocking the Secrets of Mineral Separation
Flotation, a vital process in metallurgy, plays a crucial role in extracting valuable minerals from ores. With its wide-ranging applications in the mining industry, understanding the principles and techniques of flotation is essential. In this blog post, we will delve into the intricacies of the flotation process, exploring its history, principles, equipment, and environmental considerations.
Principles of Flotation in Metallurgy
Flotation, a fundamental process in metallurgy, involves the separation of minerals from the surrounding gangue by utilizing their unique surface properties. Understanding the principles underlying this process is essential for successful mineral separation. In this article, we will explore the key principles of flotation in metallurgy.
Hydrophobicity and Hydrophilicity:
Flotation relies on the inherent differences in the hydrophobic (water-repellent) and hydrophilic (water-attracting) properties of minerals. Through selective attachment to air bubbles, hydrophobic minerals can be separated from the hydrophilic gangue.
Collectors:
Collectors are chemical reagents that enhance the hydrophobicity of minerals, promoting their attachment to air bubbles during flotation. These collectors selectively bind to the mineral surfaces, making them less water-attractive and more inclined to adhere to air bubbles.
Frothers:
Frothers are vital in generating and stabilizing a froth layer during flotation. By reducing the surface tension of the water, frothers facilitate the formation of small air bubbles, which carry the hydrophobic minerals to the surface for recovery.
pH Control:
pH plays a crucial role in flotation as it affects the mineral surface charge and the solubility of reagents. Optimal pH conditions are determined based on the mineral species being targeted, as different minerals exhibit different flotation responses at varying pH levels.
Particle Size and Liberation:
Particle size and liberation have a significant impact on flotation efficiency. Finely ground particles provide a larger surface area for interactions with collectors and air bubbles, while proper liberation of valuable minerals from the gangue ensures their effective recovery.
Air Dispersion and Agitation:
Efficient air dispersion and agitation within the flotation cell are essential for maximizing the contact between minerals and air bubbles. Proper mixing and agitation promote the distribution of air bubbles throughout the pulp, enhancing the probability of mineral-bubble collisions.
Selective Flotation:
Selective flotation aims to separate specific minerals from complex ore mixtures. This is achieved through the adjustment of reagent dosages, pH levels, and other operational parameters to target the desired minerals while minimizing the recovery of unwanted components.
Flotation Circuit Design:
The design of flotation circuits involves the arrangement and configuration of multiple flotation cells to achieve the desired separation efficiency. Factors such as cell size, arrangement, and residence time are carefully considered to optimize the flotation process.
By understanding these fundamental principles, metallurgists can tailor flotation processes to specific ore types, maximizing the recovery of valuable minerals while minimizing operational costs. Continuous research and innovation in flotation technology contribute to advancements in efficiency and sustainability in the field of metallurgy.
Flotation Equipment and Components
Flotation systems consist of various components, including flotation machines, frothers, collectors, and modifiers. Different types of flotation machines, such as mechanical cells or flotation columns, are used to create the necessary conditions for mineral separation. Frothers help in generating stable froth, while collectors and modifiers aid in selectively attaching minerals to the air bubbles.
Steps in the Flotation Process
The flotation process is a widely used method for separating minerals from their ores. It relies on the differences in surface properties of the minerals to be separated. Here are the steps involved in the flotation process:
Grinding: The ore is first crushed into a fine powder through the process of grinding. This step increases the surface area of the ore, allowing for better interaction with the flotation reagents.
Conditioning: The ground ore is then mixed with water and various chemical reagents in a conditioning tank. The purpose of conditioning is to create a suitable environment for the flotation process. Reagents such as collectors, frothers, and modifiers are added to promote the selective attachment of the desired mineral particles to air bubbles.
Froth Flotation: The conditioned ore slurry is introduced into a flotation cell or a series of cells. Air bubbles are then dispersed throughout the cell, either through mechanical agitation or by injecting air directly into the pulp. The hydrophobic mineral particles, those that have a natural affinity for air bubbles, attach to the bubbles and rise to the surface, forming a froth layer.
Froth Laundering: The froth layer containing the valuable minerals is skimmed off from the flotation cell using paddles or mechanical devices. This froth, which also contains the captured gangue minerals, is then collected and transferred to a separate tank for further processing.
Concentrate and Tailings: The froth collected in the previous step is called the concentrate. It contains a high concentration of the desired mineral and is further processed to obtain the final product. The remaining slurry, known as tailings, contains unwanted gangue minerals and is typically discarded or subjected to further treatment to extract any remaining valuable minerals.
Dewatering: Both the concentrate and the tailings undergo a dewatering step to remove excess water. This can be achieved through processes such as filtration or drying, depending on the specific requirements of the mineral processing plant.
Reagent Recovery: In some cases, the flotation reagents used in the process can be recovered and reused. This is often done through additional stages of separation, such as froth flotation of the reagent-rich water or precipitation methods.
It's important to note that the flotation process is highly complex and can vary depending on the specific ore type and desired minerals. The selection of appropriate reagents and operating conditions is crucial to achieve efficient separation and maximizing the recovery of valuable minerals. Continuous research and development efforts are aimed at improving the effectiveness and sustainability of the flotation process in various industries, including mining and mineral processing.
Types of Flotation Techniques
Froth flotation is the most widely used technique due to its versatility and effectiveness in separating minerals. However, there are other variations of flotation techniques, including:
-
Column flotation
-
Dissolved air flotation
-
Hybrid methods
Each with its own advantages and specific applications.
Factors Affecting Flotation Efficiency
Several factors influence the efficiency of the flotation process. Ore characteristics, such as mineral composition and particle size distribution, significantly impact flotation performance. Additionally, variables like pH, temperature, and flotation time play a crucial role in achieving optimal recovery rates.
The optimization of the flotation process comes with its own set of challenges. Overcoming issues related to mineral complexity, flotation kinetics, and water quality requires continuous research and technological advancements. Emerging trends, including the use of data analytics and automation, offer promising opportunities for improving flotation efficiency.
Environmental Considerations in Flotation
While flotation is a critical process in metallurgy, its environmental impact cannot be overlooked. Efforts are being made to mitigate these impacts by recycling and reusing flotation reagents and adopting sustainable practices. Responsible flotation techniques aim to minimize the use of harmful chemicals and reduce water and energy consumption.
Applications of Flotation in Different Industries
The applications of flotation extend beyond traditional metal extraction. Flotation plays a vital role in various industries, including base metal extraction (copper, lead, zinc), precious metal recovery (gold, silver, platinum), and even non-metallic mineral processing such as coal and phosphate beneficiation.
Conclusion
Flotation stands as a cornerstone of the metallurgical industry, enabling the extraction of valuable minerals from complex ores. By understanding the principles, equipment, and factors influencing flotation efficiency, we can unlock the secrets of mineral separation. As research and technological advancements continue, the flotation process will evolve, enabling more efficient and sustainable mineral extraction for future generations.
Leave A Reply
Your email address will not be published. Required fields are marked *
0 Comment