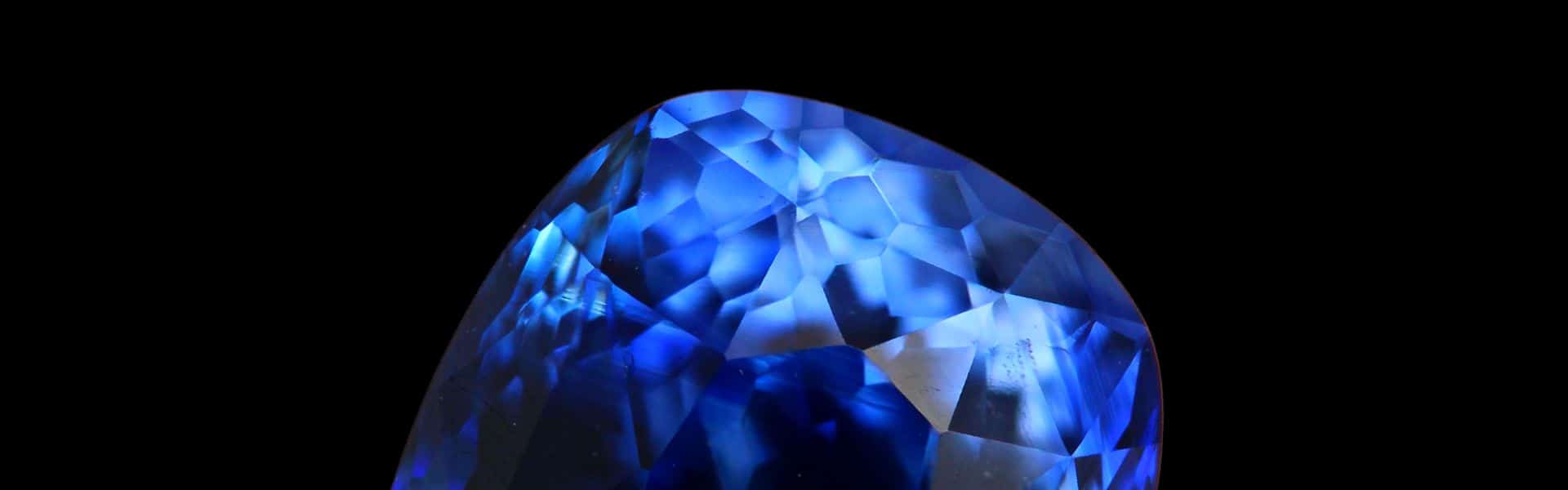
Unveiling Firescale: Understanding its Impact on Metalwork
Firescale, an unwelcome phenomenon in the realm of metalworking, has the potential to mar the beauty and integrity of crafted metals. In this blog post, we embark on a journey to explore the intricacies of firescale, its causes, preventive measures, and its significance in various metalworking industries. By unraveling the mysteries surrounding firescale, we equip ourselves with the knowledge to create impeccable metalwork while preserving its quality and aesthetic appeal.
Understanding Firescale
To comprehend firescale, we must delve into its nature and formation. Firescale refers to the reddish or dark oxide layer that forms on the surface of metals during high-temperature heating processes. This layer detracts from the intended appearance of the metalwork, often requiring additional efforts for removal or mitigation. Firescale can compromise the quality and visual appeal of jewelry, sculptures, and other metal objects, making it crucial to understand its causes and implications.
Causes of Firescale
Firescale is primarily caused by the interaction of oxygen with metals during heating. As metals are exposed to elevated temperatures, oxygen infiltrates the surface, leading to the formation of oxides. Factors such as prolonged heating, insufficient flux or protective coatings, and improper surface preparation can exacerbate the development of firescale. Alloy composition and the presence of impurities also play a role in firescale formation, highlighting the complexity of this phenomenon.
Preventing Firescale
Prevention is the key to combating firescale and ensuring the desired outcome of metalwork. Several techniques and precautions can be employed to minimize its occurrence. Proper flux application, which acts as a barrier against oxygen, is essential during metalworking processes. Utilizing protective coatings, such as boric acid or flux-based compounds, can effectively shield metals from oxygen infiltration. Additionally, working in controlled atmosphere environments, such as using reducing atmospheres or protective gases, can significantly reduce the formation of firescale.
Removing and Minimizing Firescale
In cases where firescale has already formed, various methods can be employed to remove or minimize its presence. Mechanical techniques such as sanding, filing, or buffing can be utilized to eliminate superficial firescale. Chemical treatments, such as pickle solutions or acid baths, can also aid in the removal of firescale. Metal finishing and polishing techniques play a crucial role in minimizing firescale by refining the surface and enhancing its appearance.
Firescale in Specific Metals
The manifestation of firescale varies depending on the type of metal being worked on. For instance, silver is particularly prone to firescale due to its composition and high reactivity with oxygen. Copper, known for its vibrant red hue, is also susceptible to firescale formation. Gold, on the other hand, exhibits a lower tendency for firescale but is not entirely immune. Understanding the unique challenges and preventive measures associated with each metal type enables artisans to create metalwork with minimal firescale-related issues.
Firescale and Jewelry Making
The impact of firescale on jewelry making cannot be underestimated. Jewelry artisans strive for perfection, and firescale can pose significant challenges in achieving flawless results. Preventive measures, such as proper flux application, careful temperature control, and meticulous surface preparation, are essential in the jewelry making process. Awareness of firescale and its implications empowers jewelry makers to create exquisite pieces that endure the test of time.
Firescale and Metalworking Industries
Firescale extends its reach beyond jewelry making and finds relevance in various metalworking industries. Blacksmithing, silversmithing, metal casting, and other sectors all encounter firescale-related challenges. The presence of firescale can impact production efficiency, product quality, and the overall success of metalworking endeavors. Adhering to best practices, industry standards, and continuous research and development are
Leave A Reply
Your email address will not be published. Required fields are marked *
0 Comment