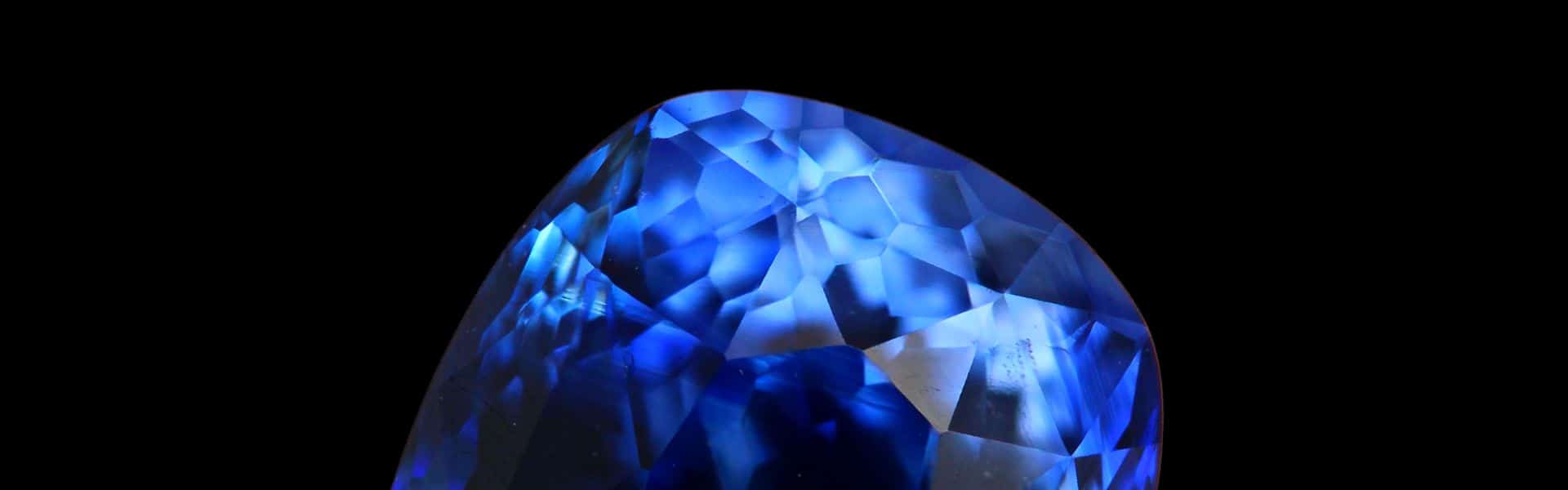
The Art of Transformation: Unveiling the Jewelry Casting Process
Jewelry casting is a centuries-old technique that allows artisans to transform molten metal into exquisite pieces of wearable art. This blog post explores the intricate process of jewelry casting, highlighting the steps involved and the craftsmanship behind it.
The Foundation: Creating a Master Pattern
Crafting the perfect piece of jewelry begins with creating a master pattern. This prototype serves as the foundation for the final piece, guiding the entire casting process. Artisans employ various methods to create the master pattern, including hand-carving, 3D printing, or using pre-made components. Regardless of the technique, precision and attention to detail are paramount in capturing the desired design and intricacies.
Preparing the Mold
Once the master pattern is complete, the next step is preparing the mold. This process involves creating a negative impression of the master pattern, allowing for the replication of the design in molten metal. Artisans use different mold materials, such as rubber, silicone, or investment plaster, depending on the specific requirements of the piece. The quality of the mold directly impacts the final outcome, so meticulous care is taken to ensure flawlessness.
Setting Gemstones and Final Touches
For pieces that incorporate gemstones, the setting process follows the finishing stage. Artisans carefully choose the appropriate setting style, such as prong, bezel, or pave, to secure the gemstones onto the jewelry piece. The setting not only enhances the beauty of the gemstones but also provides structural integrity. Additionally, artisans may add other final touches, such as engraving, plating, or attaching decorative elements, to further personalize and enhance the piece's design.
Selecting the Metal Alloy:
The choice of metal alloy for casting depends on various factors such as the desired characteristics of the final piece, its intended use, and the aesthetic preferences of the artisan or client. Common metals used in jewelry casting include gold, silver, platinum, and their respective alloys. Each metal possesses unique properties that contribute to the final appearance, durability, and value of the jewelry.
Before the casting can commence, the chosen metal alloy must be melted down to its liquid form. This is typically achieved using a specialized melting furnace, where the metal is subjected to high temperatures until it reaches its melting point. Precise temperature control is essential to prevent overheating or underheating, as it can affect the quality and integrity of the final piece.
The Casting Process:
With the molten metal prepared, the casting process can begin. There are different methods of casting, including centrifugal casting and vacuum casting, each with its own advantages and considerations. In centrifugal casting, the mold containing the wax pattern and sprue are securely attached to a centrifugal casting machine. When the molten metal is poured into the mold, the machine is rapidly spun, exerting a centrifugal force that ensures the metal is evenly distributed throughout the mold cavity. This method helps minimize porosity and produce consistent results.
Vacuum casting, on the other hand, involves creating a vacuum-sealed environment around the mold. As the molten metal is poured into the mold, the vacuum draws out any air bubbles or impurities that may be present, resulting in a cleaner and more precise casting.
During the casting process, it is crucial to pour the molten metal carefully and at the appropriate temperature. The metal flows into the mold through the sprue, filling the void left by the melted wax. The success of the casting relies on the artisan's skill in controlling the metal's flow, ensuring that all areas of the mold are adequately filled.
Once the molten metal has been poured into the mold, it begins to cool and solidify. The cooling time depends on various factors, including the metal type, thickness of the piece, and ambient conditions. It is essential to allow sufficient time for the metal to solidify completely to avoid any deformation or flaws in the final piece.
Lost-Wax Casting Technique
The lost-wax casting technique is one of the most commonly employed methods in jewelry casting. It involves a series of precise steps that bring the design to life. First, the master pattern is attached to a sprue, a pathway through which the molten metal will flow. The pattern, along with the sprue, is then invested in a material that can withstand high temperatures. During burnout, the mold is heated, causing the wax to melt away, leaving a hollow space. Finally, molten metal is poured into the mold, filling the void left by the melted wax
Is the Jewelry casting process still popular?
The jewelry casting process remains a popular and widely used method in the jewelry industry. It offers several advantages, including the ability to create intricate and complex designs, reproduce multiple copies of a design, and work with a variety of metals and alloys. The craftsmanship and artistry involved in jewelry casting continue to be highly valued by artisans and customers alike.
While there have been advancements in technology and alternative manufacturing methods, such as computer-aided design (CAD) and 3D printing, these techniques are often complementary to the casting process rather than replacements for it. CAD and 3D printing can be utilized in the initial stages of creating a master pattern, providing greater precision and efficiency in design development. However, when it comes to the actual production of jewelry, the casting process remains an integral part of the manufacturing workflow.
Jewelry casting offers unique capabilities that are not easily replicated by other methods. It allows for the creation of complex, three-dimensional designs with intricate details and fine textures. The process also enables the use of a wide range of metals and alloys, including precious metals like gold, silver, and platinum, as well as non-precious metals like brass or bronze. The versatility and flexibility of casting make it a preferred choice for jewelry production.
Moreover, the jewelry industry has a deep-rooted appreciation for traditional craftsmanship and the heritage associated with casting techniques. Many customers value the artistry and authenticity that comes with handcrafted pieces created through the casting process. It adds a sense of uniqueness and personal touch to the jewelry, enhancing its value and appeal.
While technological advancements continue to shape the jewelry industry, the casting process remains a staple due to its intrinsic qualities and the emotional connection it fosters. It preserves the age-old tradition of artisanal craftsmanship and celebrates the art of transforming molten metal into wearable art.
Leave A Reply
Your email address will not be published. Required fields are marked *
0 Comment